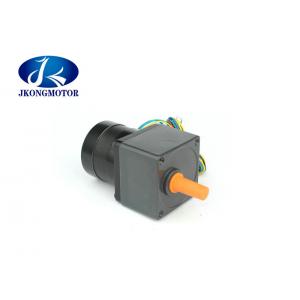
Add to Cart
184W 24V Gear Reduction Bldc Motor 3 Phase 4000RPM Brushless Dc Motor With Gear Ratio 10:1
The main parameters to be referenced in the selection of brushless DC motor are as follows:
Maximum torque: this can be obtained by adding the load torque, moment of inertia and friction. In addition, additional factors such as air gap air resistance influence the maximum torque.
Square modulus torque: can be approximately considered as the continuous output torque required for practical application, determined by many factors: maximum torque, load torque, moment of inertia, acceleration, deceleration, and running time, etc.
Speed: this is the required speed, which can be determined according to the speed trapezoidal curve of the motor, usually 10% margin should be left in the calculation.
Electrical Specification:
Model | ||
Specification | Unit | JK57BLS04 |
Number Of Phase | Phase | 3 |
Number Of Poles | Poles | 4 |
Rated Voltage | VDC | 36 |
Rated Speed | Rpm | 4000 |
Rated Torque | N.m | 0.44 |
Rated Current | Amps | 6.8 |
Rated Power | W | 184 |
Peak Torque | N.m | 1.32 |
Peak Current | Amps | 20.5 |
Back E.M.F | V/Krpm | 7.1 |
Torque Constant | N.m/A | 0.068 |
Rotor Inertia | g.c㎡ | 230 |
Body Length | mm | 107 |
Weight | Kg | 1.25 |
Sensor | Honeywell | |
Insulation Class | B | |
Degree of Protection | IP30 | |
Storage Temperature | -25~+70℃ | |
Operating Temperature | -15~+50℃ | |
Working Humidity | 85% or under 85% RH(non condensing) | |
Working Environment | outdoor(no direct sunlight),Non-corrosive Gas, Non-inflammable gas, No oil fog, No dust | |
Altitude | 1000m or under 1000m |
Gearbox Electrical Specification:
Reduction ratio | 3 | 5 | 7.5 | 10 | 15 | 18 | 20 | 25 | 30 | 50 | 60 | 75 | 100 | 120 | 150 | 200 |
Number of geartrains | 1 | 2 | 3 | |||||||||||||
Rated torque | 3 N.m | |||||||||||||||
Peak torque | 5 N.m | |||||||||||||||
length(mm) | 32 & 41 | 41 |
Products of special request can be made according to the customer request !
Ideal Applications for BLDC Motors
We’ve seen that BLDC motors offer high efficiency and controllability, and that they have a long operating life. They are widely used in devices that run continuously. They have long been used in washing machines, air conditioners, and other consumer electronics; and more recently, they are appearing in fans, where their high efficiency has contributed to a significant reduction in power consumption.
They are also being used to drive vacuum machines. In one case, a change in the control program resulted in a large jump in rotational speed—an example of the superlative controllability offered by these motors.
BLDC motors are also being used to spin hard disc drives, where their durability keeps the drives operating dependably over the long term, while their power efficiency contributes to energy reduction in an area where this is becoming increasingly important.
Toward Wider Usage in the Future
We can expect to see BLDC motors used in a wider range of applications in the future. For example, they will probably be widely used to drive service robots—small robots that deliver services in fields other than manufacturing. One might think that stepper motors would be more suitable in this type of application, where pulses could be used to precisely control positioning. But BLDC motors are better suited to controlling the force. And with a stepper motor, holding the position of a structure such as a robot arm would require a relatively large and continuous current. With a BLDC motor, all that would be required is a current proportionate to the external force—allowing for more power-efficient control. BLDC motors may also be replacing simple brushed dc motors in golf carts and mobility carts. In addition to their better efficiency, BLDC motors can also deliver more precise control—which in turn can further extend battery life.
BLDC motors are also ideal for drones. Their ability to deliver precision control makes them especially suited for multirotor drones, where the drone’s attitude is controlled by precisely controlling the rotational speed of each rotor.