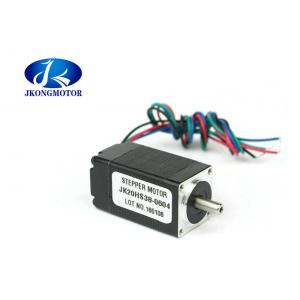
Add to Cart
180g.Cm Torque Nema 8 Stepper Motor , 20*20*30mm 0.6A 4-wire Micro Stepper Motor
Hybrid stepper motor is a combination of variable reluctance and permanent magnet motor. The stator is electromagnetically stimulated like variable reluctance stepper motor, and the rotor of the stepper motor is axially magnetized like permanent magnet stepper motor. This stepper motor is an actuator that converts electrical pulses into angular displacement.
All motors convert electrical power, volts and amps, into mechanical power, torque and speed. The unique feature of stepper motors is that they can be very accurately controlled in terms of speed and rotation angle. Stepper motors are brushless DC motors, and as such, require an electronic driver to commutate the windings. In order to control the rotation, electrical pulses are input into the driver, and the motor rotates one step for each pulse. The excellent stability of the motor results in a simple control circuit, since the motor can be run open-loop and no feedback is required.
1. Genaral Specification:
2. Electrical Specification:
Model No. | Step Angle | Motor Length | Current /Phase | Resistance /Phase | Inductance /Phase | Holding Torque | # of Leads | Motor Weight |
( °) | (L)mm | A | Ω | mH | g.cm | No. | Kg | |
JK20HS30-0604 | 1.8 | 30 | 0.6 | 6.5 | 1.7 | 180 | 4 | 0.06 |
3. Drawing:
Stepper Motor Advantages